Maiolica is a type of low-fire ceramic earthenware covered with an opaque white tin glaze and decorated with colored pigments. Maiolica pottery was especially popular in Italy during the Renaissance.

image source:Â https://search.creativecommons.org/photos/88e0164b-c377-40f7-81cf-e8229a6094be by quinet
What is a Maiolica?
Maiolica was born in the Italian Renaissance; it was white-glazed pottery. This ceramic tableware was replaced by maiolica ones, such as dishes, bowls, serving vessels, and jugs of all shapes and sizes. Maiolica was also used in sculpture and sculptural reliefs, as well as floor and ceiling tiles.
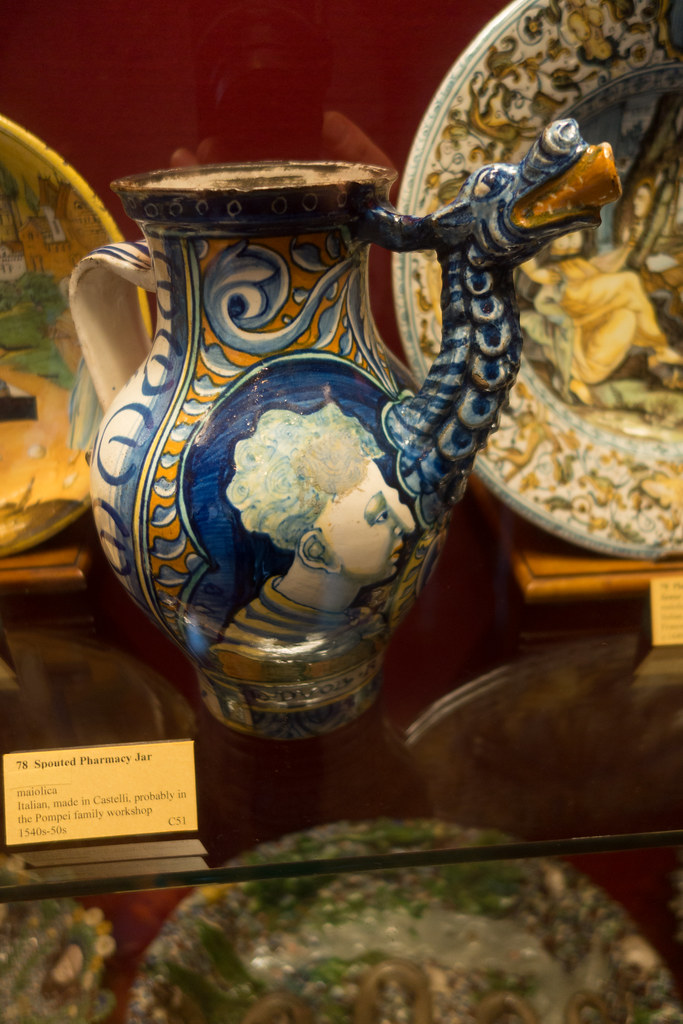
Image source:Â https://search.creativecommons.org/photos/41a877fa-688e-41cc-84a8-3f01e14e3445 by quinet
Maiolica is distinguished by its white, opaque glaze, due to the presence of tin oxide, powdery white ash. Tin was an expensive imported substance, which made maiolica a far more expensive commodity than ordinary pottery. Great care was taken to refine and shape the local clays, which varied considerably in color and weight.
The tin-glazed exterior was even and polished but not sparkling. In the sixteenth century, artisans applied a second, clear glaze to maiolica objects, which produced a brilliantly shiny surface and intensified the color design. The tin glaze was a blend of the components of ordinary lead glaze and tin oxide. This was liquefied with water and a little gum arabic, into which the clay objects were dipped. When thoroughly dry, the surface was ready to be painted, a difficult process requiring great control by the painter, as the surface in its pre-fired condition readily absorbed the pigments, themselves dry powdery metal oxides mixed with a little water and perhaps gum arabic.
Around 1430–60, the range of colors available for decorating maiolica expanded from purple-brown derived from manganese and green from copper, to blue from cobalt. By the early sixteenth century, a full range of colors was available.
Â
When Italian majolica was invented?
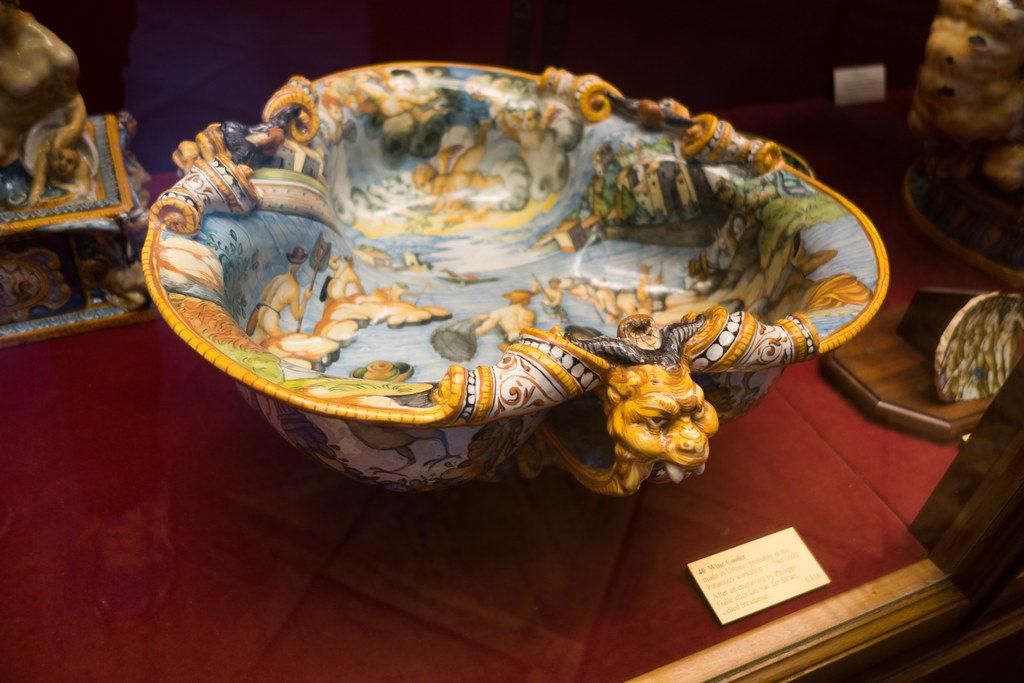
Image source:https://search.creativecommons.org/photos/103aa4e1-3e14-4662-be22-2ef389cd081b by quinet
Florence led the way in the 15th century in the production of maiolica. The production of the city workshops represented technical and aesthetic progress on the process. Before the end of the 16th century, important centers in Naples, Pesaro, Faenza, Rome, and Deruta produced precious majolica. Starting from the 16th century, surviving examples of great beauty were made in Forlì, Cafaggiolo, Castel Durante, Rome, Urbino, and Venice, as well as in various places in Sicily. The design sources were either new designs incorporating the client’s weapon and insignia for one-offs or prints and other designs often repeated in an early form of mass production.
Â
How was maiolica made?
Maiolica is made by first sourcing clay from the earth and kneading it into a consistent mass to eliminate air. To begin forming the clay into a shape, also known as the process of “throwing,” potters use a spinning circular platform. This device has a circular base which the potter controls by foot to keep a consistent speed. The potter centers the clay on the spinning wheel, exerting pressure by hand to form the shape of the clay object. Sometimes molds are used to duplicate an existing ceramic design like a plate. When throwing clay using a mold, the potter will first center the mold on the wheel, and then center the clay mass over the mold and press it into the mold. Potters sometimes rest their hands on a bar extended over the wheel to keep them steady while removing excess clay to make it uniform over the mold.
Once the clay is formed into the desired shape, it is fired in a kiln. A kiln is an extremely hot oven used specifically for hardening ceramics. Traditional kilns were heated with a wood-burning fire. Fires produce ash, smoke, and gas, which can damage vessels. To avoid such damage, Renaissance potters would place fine vessels inside a special refractory clay container that better withstood extremely high temperatures. After the ceramic object is removed from the kiln and cools, it is coated in a white tin glaze. This creates the opaque white ground that maiolica is known for. Sometimes an artist’s fingerprints are visible in the white glaze, usually at the base of the ceramic object where it was held to dip into the glaze.
When the white glaze is dry, paint is added to the ceramic object. Renaissance potters were limited to mainly blue, green, and earth-toned pigments. When finished with the decoration, the potter fires the work a second time in the process known as the “gloss firing.” This fuses the glaze and pigments to vessels, giving maiolica its distinct glass-like finish and preserving its bright colors.
Â
How was maiolica used?

image source: https://search.creativecommons.org/photos/85846bb8-ea32-4f5d-8a62-26176e327359 by fboudville
The majority of maiolica produced during the Renaissance was intended for practical use.
Tableware like plates, bowls, and jugs was quite common, as were tiles, inkwells, candlesticks, and devotional reliefs. Maiolica drug jars, like the piece at the left, were also commonly used to store herbs and medicines.
Â
How were Renaissance majolicas decorated?
The decoration of the majolica varied according to the tastes and traditions of the country that produced it and according to the needs of the client. The dishes could be decorated with heraldry, religious scenes, or animal or plant motifs. The entire outer surface of a plate or pot could be covered with very colorful narrative scenes known as istoriato or “story-painted” majolica. The stories depicted, often stemming from ancient mythology, the Bible, or classical history, were in high demand. The entire series of istoriato majolica was ordered by wealthy Italian families. One set was ordered by Eleonora Gonzaga as a gift for her mother, Isabella d’Este, in 1524. During the 16th century, the best Italian majolica such as istoriato was regularly commissioned by or for the richest, oldest, and most demanding of the time, both Italians and foreign.
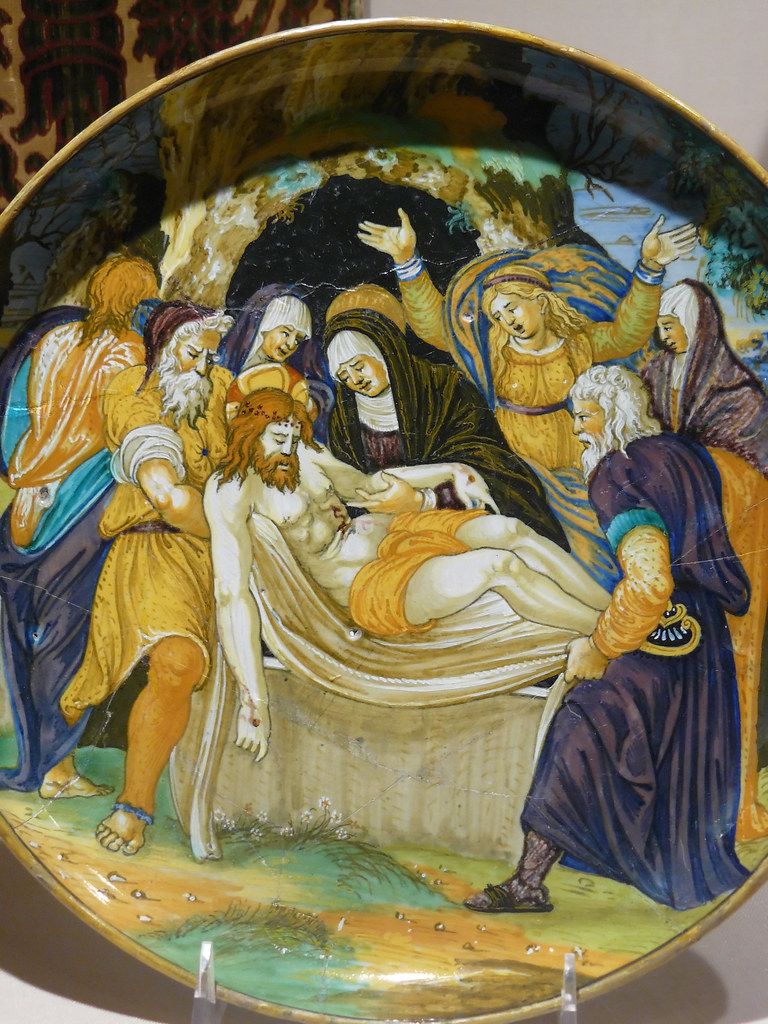
image source: https://search.creativecommons.org/photos/952fdc04-28fa-4ebd-b4d8-a9aa5be58179 by mharrsch
Â
How many type of pottery are there?
Pottery is a decorative or useful item hardened by heat clay. Based on the clay type and the temperature for hardening, pottery has a different appearance and strength.
There are three major pottery types:
- Earthenware is also known as bisque or biscuit. It is usually reddish or white. It doesn’t need a high temperature when fired (1800° to 2100° Fahrenheit). Because of its high porosity, earthenware must be glazed to allow it to hold water. Some Earthenware pieces were discovered, dating back to 1400-1200 BC, making this craft the oldest pottery in history.Â
- Stoneware is created of a heavier clay mixture, which has to be fired at high temperatures – 2200° to 2400° Fahrenheit. It is thick, impermeable, and hard enough to resist scratching by a steel nib. It’s brownish-grey and it can be used both glazed and unglazed. Ideal for cooking and baking.
- Porcelain is produced from a particular clay that contains kaolinite. The temperature needed is 2200° to 2500° Fahrenheit. It is strong, impermeable, white, and translucent.

Image source:Â https://search.creativecommons.org/photos/9abc3192-69ea-4629-a773-9c64b5287d9c
- Majolica is made of tin-glazing earthenware and needs a second firing. After the first firing, the bisque is dipped into a fast-drying liquid polish. When dry, the glazed piece is ready to be hand-painted. A final firing at 1690° Fahrenheit makes the polish mix with the metal oxides in the painting to produce intense and brilliant crystalline colors specific to majolica.
Â
Info sources:
http://www.metmuseum.org/toah/hd/maio/hd_maio.htm https://www.khanacademy.org/partner-content/getty-museum/getty-decorative-arts/a/maiolica-history-function-and-production  http://www.lagazzettaitaliana.com/history-culture/7881-maiolica https://www.thatsarte.com/blog/highlights/the-difference-between-pottery-ceramics-and-majolica-with-special-regard-to-italian-ceramics/